Management Training
- Training
- Management Training
THE EXECUTE PROGRAM
A Lean Management Training leading to significant results
Management has an important role in transferring the principles and values described in booklets and power point presentations into action and behavior. An effective way of transferring such documents into behavior is to work with practical training.
The purpose of this training program is to strengthen the knowledge and skills of top management to perform and empower continuous improvements. It will give the managers a better understanding of what the managements role is and what behavior is needed.
The focus is on some fundamental “cornerstones” in a lean operations system. The training will give good possibility to share common things and align thinking within your business, so that all people will have the same view of what needs to be done to reach a culture of continuous improvements and in the end have a more successful business.
- Adaptable to company needs
- Each participant or participating site works with own pilot area in the program = direct result
- Homework and coaching between modules
- Proven program outline – references from large global companies
- Run with multi-sites and countries
- Productivity result increase at participating sites: 15-30 % within 6 months after finished program
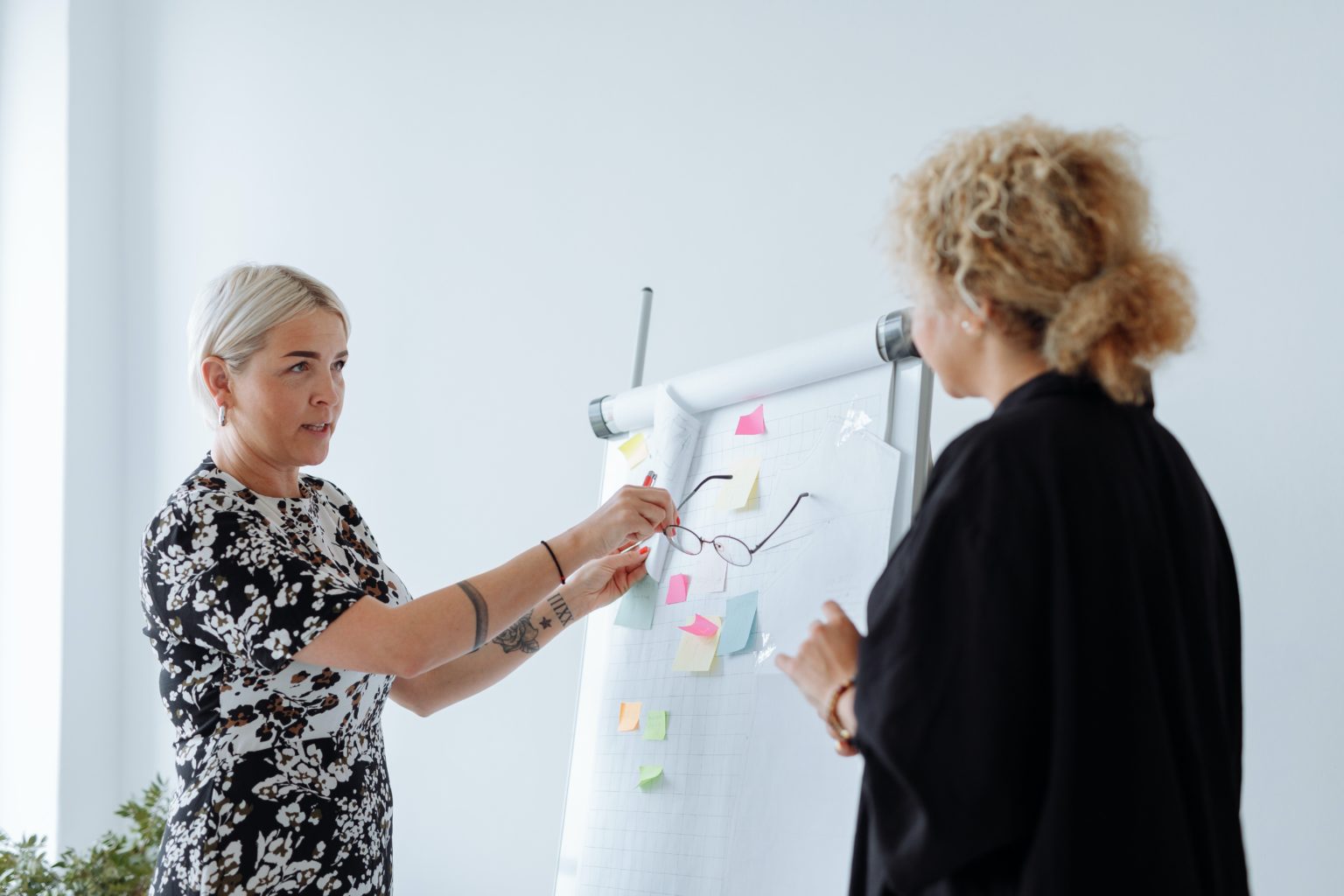
Our coaches
MODULE 1
Lean
Leadership
Factory
Leaders need to take an active role in driving the improvement process in order to reach company goals.
Stable process through Takt Time
Visual Management System
Process Management
Improvement Management through Strategy Deployment and Continuous Improvement
MODULE 2
Standardization & Visualization
Lean Training Center
To build a platform for stable, efficient and capable processes. This module will show the capability for improvements and build-up a long-term stability in order to reach world-class.
Standardized Work with Job Element Sheets, Standard Operation Sheets, Work Balancing, Heijunka and Operator Training
Visualization
MODULE 3
Systematic Problem Solving
Factory
To work with identifying deviations from standards, using a systematic approach to solve problems. Focus on real management attitude/behavior to get the most out of the organization regarding problem solving.
Systematic Problem Solving Techniques
Root Cause Analysis
MODULE 4
Strategy
Deployment
Factory
Hoshin Kanri is the way to work with policy deployment. It is a systematic way to connect targets for different levels with concrete activities in order to reach company goals.
Policy Deployment
Action Deployment Technique
Gap Analysis
MODULE 5
Continuous
Improvements
Factory
Continuous Improvement module is to strive for world-class by using the goals set in the Hoshin Kanri process to achieve a target-controlled improvement work.
Improving a Work Place
Efficient Layouts
Organization Issues
Material Handling Principles
optional
Benchmark
study visit
Optional
How other companies are working to become world class.
- Plant Visit
- Group Assignment
- Reflections
A visit to a company that have come to a higher level in applying the Lean principles.